
“How will we live together?” This is the central question for this year’s Biennale Architectura in Venice. The University of Stuttgart’s IntCDC Cluster of Excellence has responded to it with radically new fiber construction methods.
Ethereal architecture in the form of a transparent multi-story and feather-light web of fiber: “the Maison Fibre” almost seems to float. Presented by the Institute for Computational Design and Construction (ICD) and the Institute of Building Structures and Structural Design (ITKE) as part of the Arsenal of the 2021 Biennale Architectura in Venice, the Maison Fibre gives visitors the spatial experience and leaves them with the structural impression of a “building” whose structural elements can be made from just a few kilograms of material, sometimes even directly on site.
Both are urgently needed to get on top of the major environmental and sociological challenges involved in construction work because, at this moment, it is common practice to purchase ease of construction at the cost of additional material requirements: hardly any other human activity consumes more resources and releases more emissions than construction work, so new conceptual paradigms are urgently needed. “Our entry to the Biennale calls prevailing material-intensive construction methods into question and replaces it with a fiber-based architecture that uses only a fraction of the building materials and opens up completely new design possibilities,” says architect Prof. Achim Menges, the spokesperson for the University of Stuttgart’s Integrative Computer-Based Design and Construction for Architecture Cluster of Excellence (IntCDC) and head of the ICD.
Our entry calls prevailing material-intensive construction methods into question.
Prof. Achim Menges
“Compared to Le Corbusier’s Maison Dom-Ino, a highly influential model for 20th-century architecture, the Maison Fibre’s weight is reduced by a factor of fifty, thus opening the doors to a new material culture.” Not only will this encompass architecture, but also the related ecological (materials and energy), economic (value creation chains and knowledge production), technical (digital technologies and robotics), and sociocultural issues.
The world's first multistory fiber structure
This paradigm shift was inspired by nature: nearly every biological load-bearing structure is constructed from fibers whose orientation, direction and density are matched precisely to the forces acting upon them. This makes them simultaneously differentiated, functional and resource-efficient. Research into the biomimetic principle of “less material through more form” has been conducted at the University of Stuttgart for many years and has been showcased, among other things, in several exhibition pavilions that have received worldwide attention. For the first time, the researchers are now applying their acquired experience with robotically manufactured fiber composite structures to load-bearing multi-story ceiling and wall construction elements. “The Maison Fibre,” as Menges emphasizes, “is the first multi-story fiber structure of its kind. It is based on an extremely lightweight, digital construction system made up entirely of fibers. Just a few years ago, it could neither have been designed nor manufactured.”
From the industrial into the architectural sector
The entire structure consists of so-called rovings, i.e., bundles of endless, unidirectional fibers. A robotic winding process with industrial roots, which was developed by the two institutes, is used to manufacture the load-bearing wall and ceiling elements. In industrial settings, this “filament winding” method is used to produce elongated, rotationally symmetrical components such as pipes. The process involves using a winding machine to deposit fibers on a rotating cylindrical core.
However, as Christoph Zechmeister,a doctoral student at the ICD, explains, applying this method to architecture raises a problem: “The shape of the component relates directly to the shape of the core. This is fine in a low-cost mass production context, but we need more flexibility in architecture, which is why we already wondered whether the core could simply be left out of an earlier fiber pavilion.” The idea worked, so the researchers at ICD and ITKE now stretch the fibers freely across a framework. “The form-giving parameters are the shape of the frame as well as the fibers themselves,” Zechmeister explains. “The first fibers form the support structure for the subsequent ones.” The robot-assisted winding process is fully automated. “We only intervene to change the material or operate the robot.”
Not only does the continuous molding process allow for a large degree of design freedom, but it also ensures an extremely low material consumption level, whereby the researchers take advantage of the so-called anisotropy phenomenon, i.e., the fact that fibers have different properties in different directions, which means that they can be matched to the respective requirements in a very differentiated manner. For example, the comparatively heavy carbon fibers are only used where they are really needed for load transference purposes, and the fiber thickness also depends on the respective stress loads. The production of a load-bearing floor element, for example, only requires a material volume of less than two percent of the component volume.
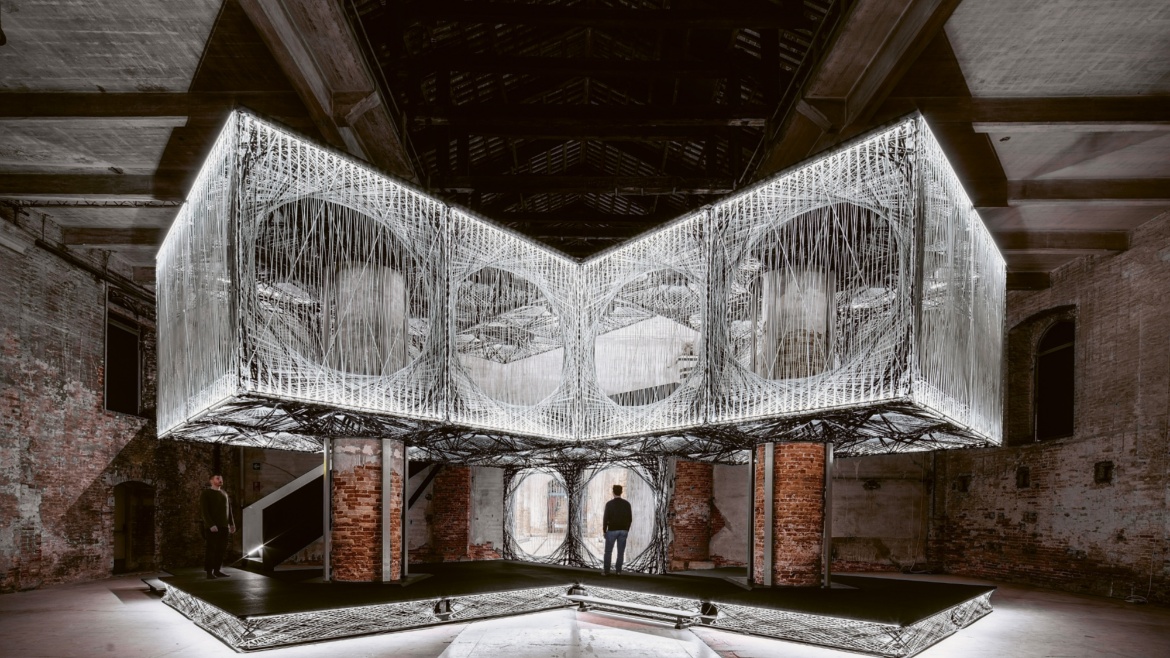
Facilitating complete on-site production
The sparing use of materials pays off: the fiber structure weighs many times less than a comparable concrete structure – the load-bearing fiber structure of the floor elements on the upper floor weighs just 9.9 kg/m². The wall elements are much lighter still, which, as Prof. Jan Knippers, one of the directors of the IntCDC cluster of excellence and head of the ITKE explains, has several benefits: “In future, the process will make it possible to do all the manufacturing on site without creating significant levels of noise or waste. And the extremely low weight makes installation much easier, because no heavy transport equipment, scaffolding or lifting devices are needed.”
This not only applies to the initial erection process, but also to any future extensions or conversions. So, architecture built using this construction method will remain adaptable and flexible over the long term. The Maison Fibre still uses the currently available fiber and resin systems, but the concept can be used with a wide range of materials, and the researchers are hoping that the range of materials will expand considerably in the near future. “Among other things,” as Menges and Knippers reveal, “we are currently studying mineral fiber systems that can withstand extreme temperature loads, and natural fibers that regenerate within a one-year cycle.”
Text: Andrea Mayer-Grenu
Prof. Achim Menges, University of Stuttgart, Institute for Computational Design and Construction
Telefon: +49 711 685 82786
E-Mail
Prof. Dr. Jan Knippers, University of Stuttgart, Institute of Building Structures and Structural Design
Telefon: +49 711 685 83280
E-Mail