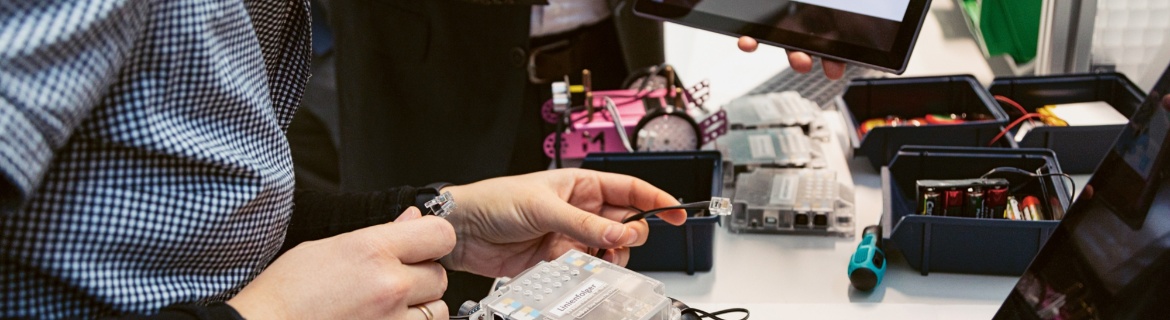
Individualisierung ist ein Megatrend, der die heutige Gesellschaft entscheidend prägt. Das zeigt etwa die gestiegene Nachfrage nach maßgeschneiderten Produkten oder Dienstleistungen. Wie finden Unternehmen heraus, ob sich eine personalisierte Produktion für ihre Produkte lohnt? Wie passen sie Produkte oder Dienstleistungen an individuelle Bedürfnisse an und produzieren dennoch kostengünstig?
Das Leistungszentrum Mass Personalization ist eine gemeinsame Initiative der Universität Stuttgart und der Fraunhofer-Institute am Standort Stuttgart. Hier entwickeln Forschende interdisziplinär und branchenübergreifend Methoden, Verfahren, Prozesse, Produktionssysteme und Geschäftsmodelle für personalisierte Produkte. „Mass Personalization“ beinhaltet eine neue, ganzheitliche Ausrichtung der Produktentstehung. Die Nutzenden stehen dabei im Mittelpunkt – und die personalisierten Produkte und Dienstleistungen kosten kaum mehr als Massenware.
„Unsere heutige Fertigungstechnologie ist auf Effizienz getrimmt und basiert vorwiegend auf einer hohen Uniformität von Produkten – das Credo der Massenfertigung. Und diese ist wichtig, denn sie versorgt uns mit kostengünstigen Produkten“, sagt Prof. Peter Middendorf, Sprecher des Leistungszentrums für die Universität Stuttgart. „Eine Personalisierung unter Massenbedingungen braucht also auch neue Fertigungstechnologien.“
Sonderanfertigungen für die Medizintechnik
Um die Grundlagenforschung zu Fabrikations- und Biomaterialtechnologien für personalisierte biomedizinische Systeme zu bündeln, hat die Universität Stuttgart eine Stuttgart Partnership Initiative gegründet, bestehend aus neun universitären Instituten. „Eine personalisierte Medizintechnik ist aus Sicht der Patientinnen und Patienten dringend nötig. Denn der Mensch ist kein genormtes Fertigungsstück“, sagt der Sprecher der Initiative, Prof. Günter Tovar.
Personalisierte Medizintechnik verspricht einen langfristigen, nachhaltigen Einsatz in der zukünftigen Gesundheitsversorgung und eine erfolgreiche Therapie. Mehrere Institute der Universität Stuttgart und der Fraunhofer-Gesellschaft forschen gemeinsam zum Beispiel zu individuell angefertigten Korsetten und Knorpelimplantaten. Dr. Okan Avci ist stellvertretender Abteilungsleiter für Biomechatronische Systeme des Fraunhofer-Instituts für Produktionstechnik und Automatisierung (IPA). Er und sein Team entwickeln digitale Netzwerke, Geschäftsmodelle sowie Datensysteme und etablieren digitalisierte Prozesse für die Medizintechnik. Ohne diese ist eine kosteneffiziente Herstellung von personalisierten Produkten nicht möglich.
„In der Medizintechnik braucht es zusätzlich zu den Orthopädietechniker*innen zahlreiche spezialisierte Verantwortliche wie Messtechniker*innen, IT-Expert*innen und Simulationsingenieur*innen, um zum Beispiel ein individuell für eine Patientin oder einen Patienten hergestelltes Skoliose-Korsett auf seine Wirksamkeit und seinen Tragekomfort hin zu analysieren, seine Stabilität zu prüfen und es kosteneffizient herzustellen“, erklärt Avci. Die Arbeit ist sehr zeitintensiv und teuer. Trotzdem seien die entstehenden Korsette, die ausschließlich Kinder und Jugendliche benötigen, oft klobig, steif, überdimensioniert und unkomfortabel.
Deshalb entwickeln Avci und seine Kolleginnen und Kollegen ein virtuelles Testsystem für Menschen, die ein Skoliose-Korsett benötigen, um eine verkrümmte Wirbelsäule zu korrigieren. Das Testsystem ermöglicht es, der Person das Korsett zunächst virtuell anzuziehen. Dazu werden Daten wie Größe und Bewegungsverhalten simuliert, um zu verdeutlich wie sich das Korsett verhält, wenn sich die jeweilige Person bewegt. „Wir geben die Daten des Korsetts und die Daten des Menschen in unser virtuelles Testsystem ein. Dieses berechnet und optimiert die Daten und zeigt uns, wie das finale Korsett für die jeweilige Person beschaffen sein sollte, um die bestmögliche Bewegungsfreiheit zu bieten, Druckstellen zu vermeiden und dennoch stabil genug zu sein.“
Knochen-Knorpelimplantate aus Biomaterialien
Es sind diese ausführlichen Analysedaten, die die additive Fertigung von personalisierten Produkten ermöglichen. Ein weiteres Projekt im Leistungszentrum Mass Personalization beschäftigt sich mit der additiven Fertigung von personalisierten Knorpelimplantaten. Fehlstellungen, Übergewicht oder Leistungssport können Kniearthrose verursachen. Die Patientin oder der Patient hat Schmerzen und ist in der Bewegungsfreiheit eingeschränkt. Ziel des Projekts ist es, eine durchgängige automatisierte Prozesskette vom CT-Scan zum personalisierten Implantat zu entwickeln, ermöglicht durch eine umfassende Prozessoptimierung.
Frederik Wulle vom Institut für Steuerungstechnik der Werkzeugmaschinen und Fertigungseinrichtungen (ISW) der Universität Stuttgart betreut das Projekt gemeinsam mit seinen Kolleginnen und Kollegen. Sie erforschen, wie individualisierbare biologische Knochen-Knorpelimplantate aus Biomaterialien automatisiert hergestellt werden können. Wulle ist für die additive Fertigung der Implantate mittels 3D-Druckverfahren zuständig. „Wir generieren auf Basis der biomechanischen Daten und auf Grundlage der Geometrierekonstruktion die zu druckende Geometrie.“
Die benötigten Daten stammen von den Kolleginnen und Kollegen des IPA. Dort erhalten die Forschenden mithilfe der Analysedaten des Bewegungsapparates Auskunft über Parameter wie Größe und Steifigkeit, die die personalisierten Knorpelimplantate besitzen müssen, um mit der individuellen Biologie und Biomechanik der Person optimal übereinzustimmen und eine erfolgreiche Therapieentwicklung zu ermöglichen.
Mithilfe der Daten rekonstruieren Wulle und seine Kolleginnen und Kollegen die Sollgeometrie der zu ersetzenden Fehlstelle mit computergestützter Konstruktion. Additive Fertigungsverfahren erlauben es, Objekte mit entsprechend komplexer Geometrie aus unterschiedlichen Materialien aufzubauen. Für die Fertigung der Knorpelimplantate setzen sie auf den innovativen mehrachsigen 3D-Druck. Der Vorteil der mehrachsigen Bearbeitung im Vergleich zum herkömmlichen dreiachsigen Verfahren sind die größeren Prozessfreiheiten. So kann beispielsweise der Stufeneffekt minimiert werden, der auftritt, wenn eine Kontur eines Bauteils nicht parallel oder orthogonal zur Aufbaurichtung verläuft und damit die Schräge in einzelne diskrete Schichten untergliedert wird.
Interdisziplinäre Zusammenarbeit
Die im Projekt verwendeten Knochen-Knorpelimplantate bestehen aus Biomaterialien. Das interdisziplinäre Forschungsfeld des Bioprintings verfolgt das Ziel, biomimetische Gewebestrukturen als Ersatz für erkranktes Patientengewebe herzustellen. Dabei orientieren sich die Forschenden an biologischem Gewebe und versuchen, dieses in digitalen Druckverfahren nachzubilden. Die Entwicklung, Herstellung und Überprüfung dieser Biomaterialien erfolgt am Institut für Grenzflächenverfahrenstechnik und Plasmatechnologie (IGVP) sowie am Fraunhofer-Institut für Grenzflächen- und Bioverfahrenstechnik IGB in Stuttgart. „Wir hatten die Technologie des mehrachsigen 3D-Drucks entwickelt und suchten eine Anwendung. Unsere Kolleginnen und Kollegen von der Materialentwicklung haben das Potenzial für ihre Anwendung erkannt“, sagt Wulle zu dieser interdisziplinären Zusammenarbeit.
Lohnt sich das für mich?
Auf den Trend der personalisierten Produktion reagieren immer mehr Unternehmen. Das Leistungszentrum bietet deshalb gezielte Weiterbildungsangebote für sie an. „Eine Kooperation mit uns eröffnet den Zugang zu vielfältigen Expertisen, die so sonst kaum zugänglich sind. Mögliche Kooperationspartnerinnen und Kooperationspartner können sich damit an Zukunftstechnologien herantasten“, sagt Leistungszentrum-Sprecher Middendorf.
Ob sich die personalisierte Produktentwicklung im Einzelfall lohnt, können Lesley-Ann Mathis und ihre Kolleginnen und Kollegen vom Institut für Arbeitswissenschaft und Technologiemanagement (IAT) der Universität Stuttgart beantworten. Sie haben eine Methode entwickelt, mit der Unternehmen ihr Produktportfolio systematisch auf Personalisierungspotenziale untersuchen können. Im Rahmen von Weiterbildungsseminaren des Leistungszentrums bringen Mathis und ihr Team Firmen ihre Methode bei. In Folgeprojekten bieten sie Unternehmen Potenzialanalysen für deren spezifische Produkte oder Dienstleistungen an.
Die entwickelte Methode beruht auf zwei Bausteinen: der „Product Journey“ und der „User Journey“. „Im Leistungszentrum gehen wir nutzerzentriert vor. Das heißt, unsere Methode setzt direkt bei der Nutzerin oder dem Nutzer an“, sagt Mathis. Ihre Vorgehensweise erklärt sie am Beispiel eines E-Scooters, den man sich per App für eine bestimmte Zeit und Strecke mieten kann: Bei der Product Journey analysiert die Forscherin mit den Seminarteilnehmenden, welche Zielgruppen das Produkt über den gesamten Lebenszyklus hat und welche Nutzergruppen Kontakt zum Produkt haben.
Beim E-Scooter sind das unter anderem Studierende, die damit zur nächsten Vorlesung an die Universität fahren, oder Angestellte, die vom Bahnhof zum Büro unterwegs sind. Aber auch Personen, die die Roller vormontieren, sie einsammeln und an Sammelstellen befördern oder sie letztlich recyceln, zählen zum breiten Spektrum der Nutzergruppen. Innerhalb der Product Journey werden daraus sogenannte Protopersonas erstellt. So entstehen Peter Pendler oder Sina Studentin, deren Nachnamen stellvertretend für deren Eigenschaften stehen.
Für die User Journey wird eine Zielgruppe des Produkts ausgewählt, die bei der Nutzung im Vordergrund steht. Anschließend begleiten die Teilnehmenden beispielweise Sina Studentin während ihres gesamten Kontakts mit dem E-Scooter – von der Buchung per App bis zum Stehenlassen des Rollers. „Wir analysieren die Berührungspunkte von Nutzerinnen und Nutzern mit dem Produkt und beurteilen, wo das Nutzungserlebnis verbessert werden könnte und wo Personalisierungsmöglichkeiten existieren“, sagt Mathis.
Alle Ideen werden hinsichtlich des Nutzens für den Kunden analysiert und anschließend einer Kosten-Nutzen-Bewertung unterzogen. Im Beispiel des E-Scooters könnte eine personalisierte Sprachausgabe entwickelt werden, die das Bedienen der App am Smartphone überflüssig macht, oder personalisierte Preismodelle für regelmäßige Nutzer*innen und häufig genutzte Strecken.
Der ganzheitliche Ansatz der Methode hebt die Vorteile für Unternehmen hervor: „Wir haben ein konkretes Werkzeug zur Hand, mit dem man relativ schnell und bereits im Frühstadium der Produktentwicklung identifizieren kann, ob sich ein Produkt für die Personalisierung eignet und lohnt“, so Mathis. Denn personalisierte Produkte seien nur dann erfolgreich, wenn sie wirklich einen Nutzen für Kundinnen und Kunden mitbringen.
Text: Bettina Wind
Prof. Peter Middendorf, Universität Stuttgart, Tel.: +49 711 685-62411, E-Mail